Ohio Design, located in an industrial space turned woodworking studio in San Francisco’s Mission District, is the go-to furniture fabricator for Silicon Valley’s style-conscious tech companies.
Founded in 2000 by David Pierce, who studied landscape architecture at UC Berkeley, Ohio Design is named after Pierce’s home state. Pierce’s background in landscape design has inspired his work at Ohio Design; he began with a line of outdoor furniture, and continues to operate under cradle-to-cradle and lean manufacturing principles. For Pierce, responsible manufacturing is inherent to the idea long-lasting design; an ethos seen in each detail: recyclable steel, carb-compliant and formaldehyde-free plywood, salvaged hardwoods certified by the Forest Stewardship Council, and transparent finishes like tung oil.
While a student, Pierce was a member of a drum and bugle core that marched down Market Street in SF; he’s also studied on a fellowship in London and Scotland. His ideal design is a single levitating plane without legs. “It’s about creating a quiet atmosphere that you can then overlay your life on,” Pierce says, echoing one of Dieter Rams’ Ten Principles of Good Design: “Nothing more than it needs to be.”
Ohio’s current headquarters originally housed SF manufacturing company Metkin Tool and Die, to which Pierce has paid homage by using the original shelving and pulleys. Currently, the studio is full of products from Ohio’s new Workspace line (fun fact: one of tables is bound for Remodelista’s SF office). “Gone are the days of typical workspaces,” says Pierce about his new line, which features a deliberate lack of fiberboard, melamine, or particle board (not used in any of their designs) and an adjustable-height standing desk. What’s next for Ohio? Everything from a showroom to buying trees to kiln-drying their own wood; stay tuned for more. Visit Ohio Design to see the full line of products on offer.
Photography by Jon Porras for Remodelista.
Above: The 630 Treat Avenue building features the smartly designed Ohio logo.
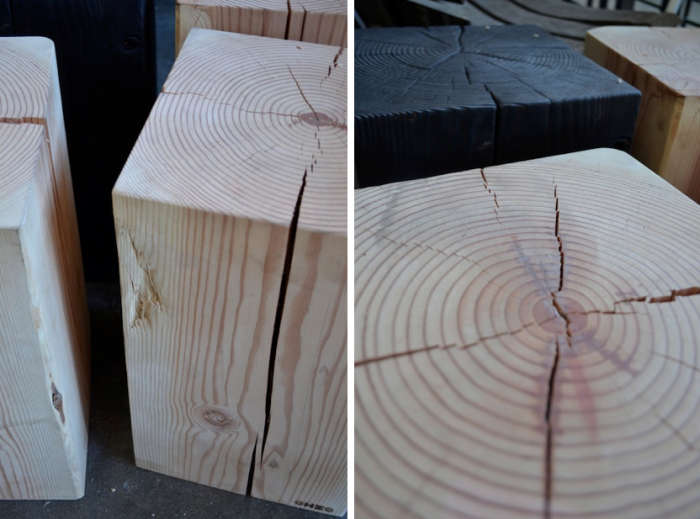
Above: Pierce designed the Blocky piece after a 1998 trip to Donald Judd’s Chianti Foundation in Marfa, Texas. The piece on the left is for a scratch and dent sale, see the standard Blocky in radiata and carbonized radiata (using the Japanese shou-sugi-ban technique) on the site; prices range from $249 to $429.
Above: Stacks of custom made three-legged barstools in white and natural wood.
Above: The hand-welded steel frame of the Alder Desk. Pierce says of the materials, “steel is cold to the touch so we use wood where it makes sense and steel where it structurally works best.” See our previous post A Standing Desk with Style.
Above: For adjusting the table’s height, the crank is made from solid steel gears and a chromed, cast iron handle.
Above: The long and open interiors of the building give way to a smaller workshop in back.
Above: A large plane of untreated wood waiting to be formed into furniture and a pair of neon powder-coated steel legs.
Above: Salvaged antique pulleys from the previous manufacturing company at the entrance of the lofted office.
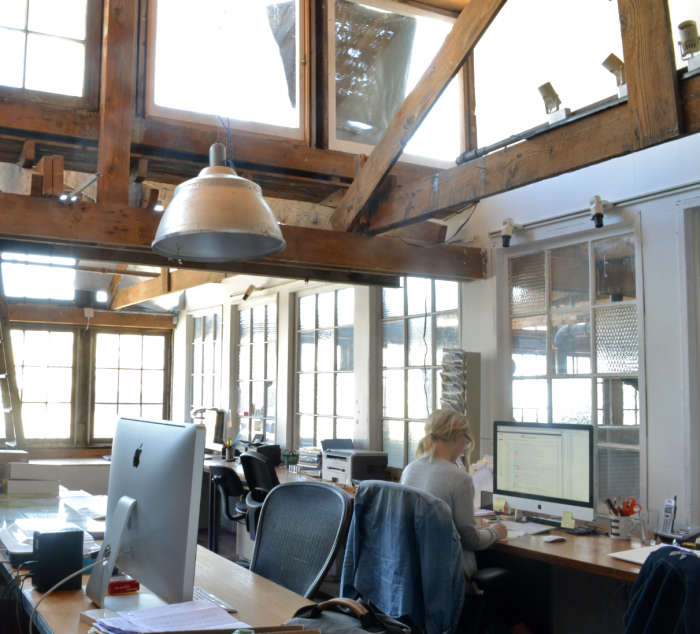
Above: The constantly evolving upstairs office space.
Above: The manufacturing workshop is located behind a pair of carbonized, sliding barn doors.
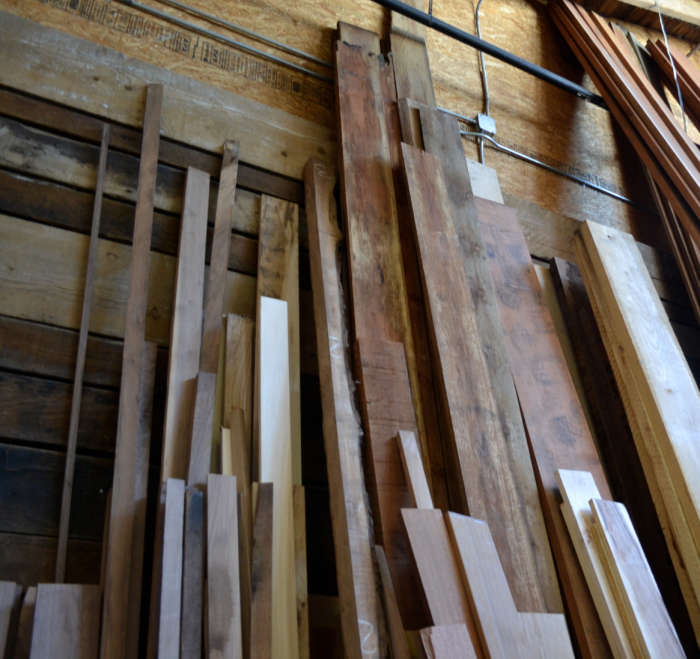
Above: As part of their lean manufacturing ethos, the company stores wood remnants that will inspire new design.
Above: Frames of soon-to-be Olia Barstools (each piece is named after the original client it was designed for); $399.
Have a Question or Comment About This Post?
(3) Join the conversation